随着智能制造的迅猛发展,增强现实(AR)技术在制造业中逐渐成为一项不可或缺的工具。AR通过将虚拟信息叠加到现实世界中,使得用户能够在实际环境中获取实时数据、指导或培训,提高生产效率、降低错误率,并增强操作的精准度。
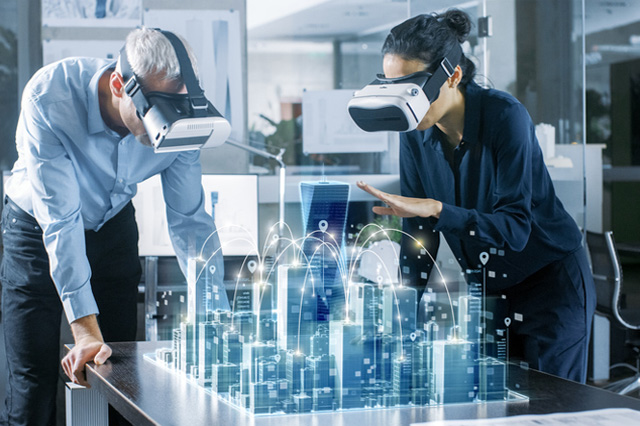
1. 明确需求与目标
AR技术的应用场景在制造业中非常广泛,包括但不限于:
产品设计与验证: 在设计阶段,AR可以帮助工程师通过虚拟模型与现实世界进行对比,验证设计的可行性,提前发现潜在问题。
装配与生产辅助: 通过AR眼镜或智能设备,操作员可以实时查看装配指导、操作步骤,甚至可以通过语音指令与系统互动,从而提高装配效率,降低错误率。
远程协作与技术支持: 在远程故障排查和技术支持中,AR可以通过视频传输实时标注,指导技术人员进行修复,减少生产停机时间。
培训与教育: 对员工进行虚拟仿真培训,减少实际操作中可能带来的风险和成本。
在开发初期,企业需要与相关技术团队、工程师和操作员进行深度沟通,明确具体的应用场景和目标,确保开发的AR系统能够解决实际生产中的问题,并满足工作流程的需求。
2. 功能分析与设计规划
明确了应用目标后,接下来的工作是进行功能分析与设计规划。这个阶段的工作内容主要包括:
需求拆解与功能模块设计: 根据应用场景,拆解出AR系统的具体功能。例如,对于装配辅助系统,功能可能包括:实时显示装配步骤、检测部件是否匹配、提醒操作人员注意安全等。对于远程支持系统,功能可能包括:实时视频、图文标注、语音指令等。
交互方式设计: AR系统需要与用户进行交互。常见的交互方式包括手势识别、语音识别、触摸控制、眼动追踪等。设计时需要考虑到使用场景和设备的限制,选择最适合的交互方式,以确保操作的流畅性和用户体验。
硬件选择: AR系统的核心硬件包括头戴设备(如Microsoft HoloLens、Magic Leap等)、移动设备(如智能手机、平板)及传感器(如深度摄像头、IMU等)。开发团队需要根据需求选择合适的硬件平台,综合考虑性能、舒适度、价格等因素。
系统架构与数据接口: 制定AR系统的技术架构,确定如何将数据与生产线设备、ERP系统等其他管理系统进行集成,以便实时获取生产数据、操作指令或工艺流程,并在AR界面中实时显示。
3. 数据采集与建模
AR系统的成功与否,往往取决于虚拟信息和现实环境的无缝融合。因此,数据采集和建模是开发过程中的核心环节。
3D建模与虚拟内容制作: 根据实际需求,创建高精度的三维模型。这些模型可能是产品组件、工厂设施、工具、设备等。开发者通常会使用CAD数据、3D扫描、物理模拟等手段生成精确的虚拟物体,并为这些虚拟物体赋予合适的物理属性,如重量、材质、体积等。
环境建模与虚拟现实: 在制造业中,AR技术常常需要将虚拟元素叠加到真实环境中。因此,开发团队需要通过环境建模,将工厂车间、生产线等场景建模进虚拟空间。为了确保虚拟信息能够准确显示,可能还需要利用空间识别、标定技术以及深度感知技术,使AR系统能够实时感知物理世界的变化。
传感器数据与实时反馈: 若AR系统需要与生产线上的实时数据交互(例如,传感器数据、设备状态等),则需要设计相应的数据接口,确保数据能够实时、准确地传输到AR系统中,并在用户界面上即时反馈。
4. 开发与集成
这一阶段是AR开发的核心部分,涉及到将前期的设计、建模和数据整合到实际应用程序中,并确保系统的稳定性和高效性。
AR应用程序开发: 基于前期的需求分析和设计规划,开发团队需要使用适合的开发平台(如Unity3D、Vuforia、ARCore、ARKit等)进行编码实现。开发的内容包括虚拟元素的渲染、用户交互的实现、数据接口的连接等。
硬件与软件集成: AR系统的硬件包括头戴设备、传感器、相机等,开发人员需要确保这些硬件设备能够与软件系统无缝配合。硬件设备的数据需要实时传输至软件进行处理,而软件的输出又需要通过硬件设备显示给用户。
实时数据处理与同步: 在生产环境中,AR应用往往需要与实时数据进行交互,例如,设备故障、生产进度、物料库存等。系统需要确保数据的实时性和准确性,以便为操作员提供及时的指导和反馈。
5. 测试与优化
在AR系统开发完成后,必须进行一系列测试,以确保系统的稳定性、性能以及用户体验。
功能测试: 确保AR系统中的所有功能按照需求正常运作。例如,检查虚拟物体的叠加效果、交互功能是否顺畅、数据接口是否准确等。
性能测试: 由于AR系统通常需要处理大量的图形渲染和实时数据,性能测试尤为重要。开发团队需要测试系统的渲染速度、响应时间、延迟等,确保AR应用在实际使用中不会出现卡顿、延迟等问题。
用户体验测试: 通过用户测试,评估AR系统的交互体验、操作的直观性和舒适度。用户反馈可以帮助开发团队发现潜在的问题,优化系统的操作流程和界面设计。
环境适应性测试: 在不同的光线、空间和生产环境下,AR系统的显示效果可能有所不同。因此,开发团队需要在多种场景中测试系统的表现,确保其在实际生产环境中能够稳定运行。
6. 部署与实施
经过充分测试与优化后,AR系统进入部署阶段。此阶段包括:
设备安装与调试: 确保AR硬件设备(如AR眼镜、平板等)能够顺利安装,并与系统连接,调试设备的传感器和显示效果。
系统集成与环境适配: 将AR系统与现有的生产管理系统(如MES、ERP等)进行集成,确保数据流畅传递。根据企业的实际需求,进行适当的环境适配和调整。
员工培训: 对员工进行AR设备的操作培训,帮助他们熟悉系统界面和使用流程,确保他们能够高效地使用AR系统。
7. 维护与持续优化
AR系统投入使用后,并不意味着开发流程就结束了。为了确保系统长期有效,企业需要进行定期的维护和更新。
系统监控与问题反馈: 监控AR系统的运行状态,及时发现并解决系统出现的故障或异常。
功能升级与扩展: 随着生产需求的变化,可能需要新增或优化现有功能。例如,增加新的虚拟元素、支持新的操作流程或设备等。
技术更新与迭代: AR技术本身在不断发展,新的硬件设备、算法或交互方式可能会带来更好的体验和效果。企业需要关注这些新技术,并适时更新系统,以保持竞争力。
AR技术在制造业中的应用,正在改变传统的生产方式、工作流程以及员工培训模式。通过与现实世界的无缝结合,AR不仅能够提高生产效率、降低错误率,还能增强员工的操作精度和技能水平。通过明确需求、功能规划、数据采集、开发集成、测试优化等一系列步骤,企业能够成功开发并实施AR应用,推动智能制造的进一步发展。随着技术的不断进步,AR将在制造业中扮演越来越重要的角色,成为未来生产的重要助力。